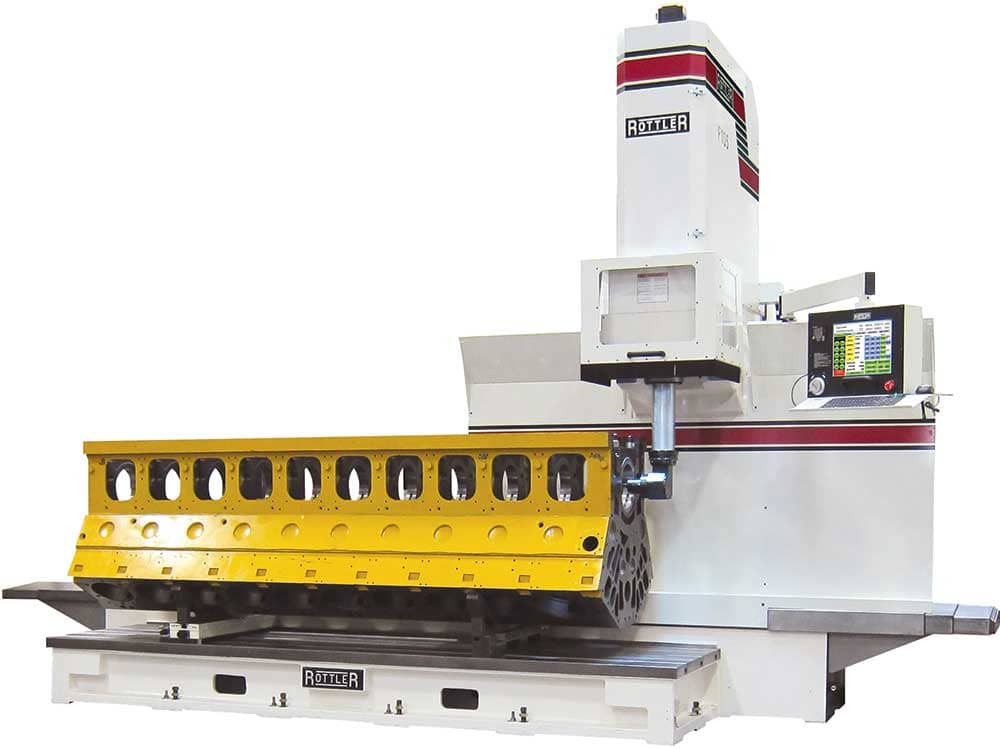
Rottler EM103H: The Ultimate Multi-Purpose CNC Machine
If you’re in the market for a versatile and high-performance CNC machine, look no further than the Rottler EM103H. As a leading CNC machine manufacturer, Rottler is known for its cutting-edge technology and precision engineering, and the EM103H is no exception.
Unleashing the Power of Multi-Purpose CNC Machining
The Rottler EM103H is a true game-changer in the world of multi-purpose CNC machines. With its advanced features and capabilities, this machine empowers manufacturers to tackle a wide range of machining tasks with unparalleled precision and efficiency.
Featuring state-of-the-art CNC technology, the EM103H offers exceptional versatility. Whether you’re involved in automotive, aerospace, or general machining, this machine is designed to meet your specific needs. Its adaptability allows you to effortlessly handle milling, drilling, boring, and other machining operations, all in one powerful unit.
Unmatched Performance and Precision
When it comes to performance, the Rottler EM103H stands head and shoulders above the competition. Equipped with a robust spindle and a rigid frame, this machine delivers outstanding stability and accuracy, ensuring consistent results with every job.
With its advanced control system, the EM103H provides seamless integration between the machine and the operator. The user-friendly interface allows for easy programming and quick setup, reducing downtime and maximizing productivity. The machine’s high-speed machining capabilities enable faster cycle times, enabling you to meet tight deadlines without compromising on quality.
Engineering Excellence and Reliability
Rottler is renowned for its commitment to engineering excellence, and the EM103H is a testament to that. Built to withstand the demands of modern manufacturing, this machine is constructed using top-grade materials and undergoes rigorous testing to ensure durability and reliability.
Additionally, Rottler offers comprehensive support and service for the EM103H. Their team of experienced technicians is always ready to assist with installation, training, and ongoing maintenance, ensuring that your machine operates at its peak performance throughout its lifespan.
Experience the Rottler EM103H Difference
If you’re ready to take your machining capabilities to the next level, the Rottler EM103H is the perfect choice. With its unrivaled versatility, performance, and reliability, this multi-purpose CNC machine empowers you to achieve exceptional results in various industries.
We have more then 100 years of experience
We have more then 100 years of experience
Features
Featues of the Rottler EM103H Traveling Column Boring Machine:
- Productivity – Up to 75% time savings over traditional machines
- Control – Touch Screen Controls located on one panel for ease of operation
- Automation – Automatically machines precise dimensions
- Flexibility – Block boring and surfacing, head surfacing, line boring and general CNC machining.
- Versatility – Change cutterheads from surfacing to boring and back in 15 seconds.
- Heavy Duty – Rottler rugged machine tool quality for accurate and long life. Heat treated mehanite cast iron castings.
- Large Diameter Spindle – All EM100 machines incorporate the use of a large diameter hard chromed spindle, utilizing high precision angular contact bearings and automatic lubrication.
- Machine ways are induction hardened and coated with turcite low friction material and supplied with air pressure to reduce friction and give long service life. Linear Roller type guideways in X- axis provide smooth and precise movement under heavy loads.
- Anti-friction Ball Screws and AC Servo motors provide precise machine positioning and rapid feed rates.
- Air power draw bar
allows cutterheads to be changed in second, increasing productivity and reducing operator fatigue. The machine can be changed from boring to surfacing in less than 15 seconds. - Automated workhead tilting system for surfacing provides “back clearance” for superior surface finish.
- Increased clearance from spindle to centerline to the machine’s column allow large castings to be set up and machined.
Machine Operations
- Automatic Tool Changer
- Block Surfacing
- Blue Print Boring
- Boring & Sleeving
- Circular Interpolation
- Connecting Rod Boring
- Cylinder Boring
- Cylinder Head Resurfacing
- Lifter Boring
- Line Boring
- Multi Purpose CNC (Custom Parts)
- Thrust Cutting
Rottler EM103H Standard Equipment
Standard equipment that comes with the Rottler EM103H Traveling Column Boring Machine:
- CNC (Computer Numerical Control) Machine using Windows Operating System and Industrial PC with Intel Processor. Precision Programming and Control thru a 19″ (483mm) Computerized Touch Screen.
- Software options available for Programmable & Automated Cycles such as Boring, Surfacing, Lower Sleeve Offset Boring, Water Hole Repairs, Main & Cam Line Boring, General CNC Machine Work
- Spindle Rotation by AC Servo Motor – Infinitely Variable 0-5000 RPM – 10HP (7.5kW)
- USB flash drive for file transfer to and from computer
- Machine/Computer can operate in either inch or metric system
- 3 Axis movement by Precision Ball Screws & AC Servo Motors – Infinitely Variable
- Horizontal Movement (X Axis) – Left and Right Direction – 80″ (2000mm)
- Horizontal Movement (Y Axis) – In and Out Direction – 16″ (406mm)
- Vertical Movement (Z Axis) – Up and Down – 29″ (736mm)
- Vertical, Horizontal and Spindle Load Monitoring for Fast Overload Shut Down
- Precision Position Display in .0001″ (.002mm) Resolution.
- Electronic Handwheel for manual movement – per click: Coarse Mode .01″(.25mm) Medium Mode .001″(.01mm) Fine Mode .0001″(.002mm)
- Infinitely Variable Feedrates adjustable by handwheel during automatic cycles
- High Performance Spindle Rotation AC Brushless Servo Motor and Drive System
- Hard Chromed Precision Spindle with High Speed Angular Contact Bearings
- Fast Rapid and Jog Speeds for Reduced Cycle Time
- Automatic Workhead Tilt System for Back Clearance during Surfacing
- Air Assisted Quick Change Cutterhead Draw Bar System
- One Piece Heat Treated Mehanite Cast Iron Machine Castings
- Air Pressurized Column for Less Friction and Accurate Positioning
- Turcite Coated Slideways for Low Friction and Extended Life
- X-axis Linear Roller Slideways for Smooth and Precise Movement.
- Automatic Central Lubrication System monitored by controller
- LED Work Light (mounted)
- Chip Guard with Adjustable Pivot Arm
- Operation, Programming and Spare Parts Manual – Digital
Give us a call, we have all the answers for you.
Rottler EM103H specifications
Control | CNC Touch Screen |
Touch Screen | 381mm |
Machine Height | 3480mm |
Table - Size | 850 x 2100mm |
Table - T Slots | 2 |
Travel - Horizontal (X Axis) | 2000mm |
Travel - In/Out (Y Axis) | 406mm |
Travel - Vertical (Z Axis) | 736mm |
Travel - Spindle Nose to Table | 1273mm |
Travel - Spindle Center to Column | 648mm |
Spindle - Rotation Speed | 0 to 1000 RPM |
Spindle - Motor | 12.75 Kw |
Cylinder Bore Range (with Optional Cutterheads) | 19 - 508mm |
Line Bore Range (with Optional Cutterheads) | 48.5 - 216mm |
Surfacing Cutterhead Diameters | 250, 360, 460 & 570mm |
Dimensions - Machine | 2134D x 2972W x 3480mm H |
Dimensions - Floor Space Requirements | 2438D x 4521Wmm |
Dimensions - Shipping | 2184D x 2972W x 2286mm H |
Machine Weight | 7257 kg |
Electrical Requirements | 208-240V, 60A, 50Hz, 60Ph |
Air Requirements | 28 l/min @ 6 bar |
Paint Color Code | RAL9002 (Grey White) |
Control
Streamlined Control with Rottler’s Conversational Programming System
At Rottler, we understand the importance of intuitive and efficient control systems in CNC machining. That’s why we’ve combined our in-house CNC programming and machining expertise with software and programming experts to develop a revolutionary conversational programming system. Our system is designed to be easy to learn and operate, ensuring a seamless experience for operators of all levels of expertise.
A User-Friendly Interface
Gone are the days of complex and abstract G&M code programming. Our conversational programming system replaces it with an easy-to-understand interface featuring Windows-style icons and graphical displays. This intuitive design makes programs easier to comprehend, reducing the learning curve for operators and enabling them to quickly grasp the functionality of the system.
With the use of familiar Windows-based features, such as file saving and copying, our control system streamlines the handling of programs. Operators can easily save and transfer programs to external laptops and desktop computers, ensuring flexibility and accessibility. Additionally, the use of standard USB flash memory drives allows for hassle-free program transfer and sharing via email or the Internet.
Efficiency with Rottler PATH CAD/CAM Software
In addition to our user-friendly control system, we offer the powerful Rottler PATH CAD/CAM Software (Computer Aided Design and Manufacturing). This software operates seamlessly in the background, performing calculations such as tool paths while the operator develops a program on the machine, laptop, or desktop.
With Rottler PATH, the software can convert a drawing into a complex CNC program with minimal operator involvement. This automation significantly reduces the time and effort required to generate intricate CNC programs, enabling operators to focus on other critical tasks. The software’s intelligent algorithms ensure precise and optimized tool paths, guaranteeing exceptional machining results.
Experience the Simplicity and Efficiency of Rottler’s Control Systems
Ready to streamline your CNC machining operations? Explore the power of Rottler’s conversational programming system and PATH CAD/CAM Software. Visit our website to learn more about our advanced control solutions and discover how they can enhance your machining processes. Harness the simplicity and efficiency of Rottler’s control systems and take your CNC machining capabilities to new heights.
ConRod Fixture
Rottler’s Connecting Rod Fixtures: Achieve Precision and Parallelism
When it comes to machining large connecting rods, Rottler has the solution. Our patented Connecting Rod Fixtures, designed for use with the EM103H machines, provide unparalleled precision and efficiency. With Rottler’s innovative boring fixtures, you can surface and bore connecting rods with ease, achieving perfect parallelism between the big end and small end.
Precision and Parallelism in One Set-Up
Our connecting rod fixtures are engineered to allow simultaneous boring of both the big end and small end in a single set-up. This unique capability ensures that the resulting center-to-center distance remains accurate and consistent across all the rods in a set. Maintaining equal center-to-center distance is vital for today’s high compression diesel engines, where precision and balance are essential.
Whether you’re working on standard-sized connecting rods or dealing with large and heavy rods found in natural gas compressors and workboat marine engines, Rottler has you covered. We offer special heavy-duty fixtures designed to handle the unique demands of these challenging applications.
Unleash the Potential of Rottler’s Connecting Rod Fixtures
Experience the power and precision of Rottler’s Connecting Rod Fixtures. By incorporating our patented fixtures into your machining processes, you can achieve unmatched parallelism, precision, and center-to-center distance accuracy in your connecting rod bore operations.
Visit our website to learn more about Rottler’s connecting rod fixtures and their compatibility with the EM103H machines. Discover how these fixtures can revolutionize your machining capabilities and help you deliver exceptional results in the automotive, marine, and natural gas industries.