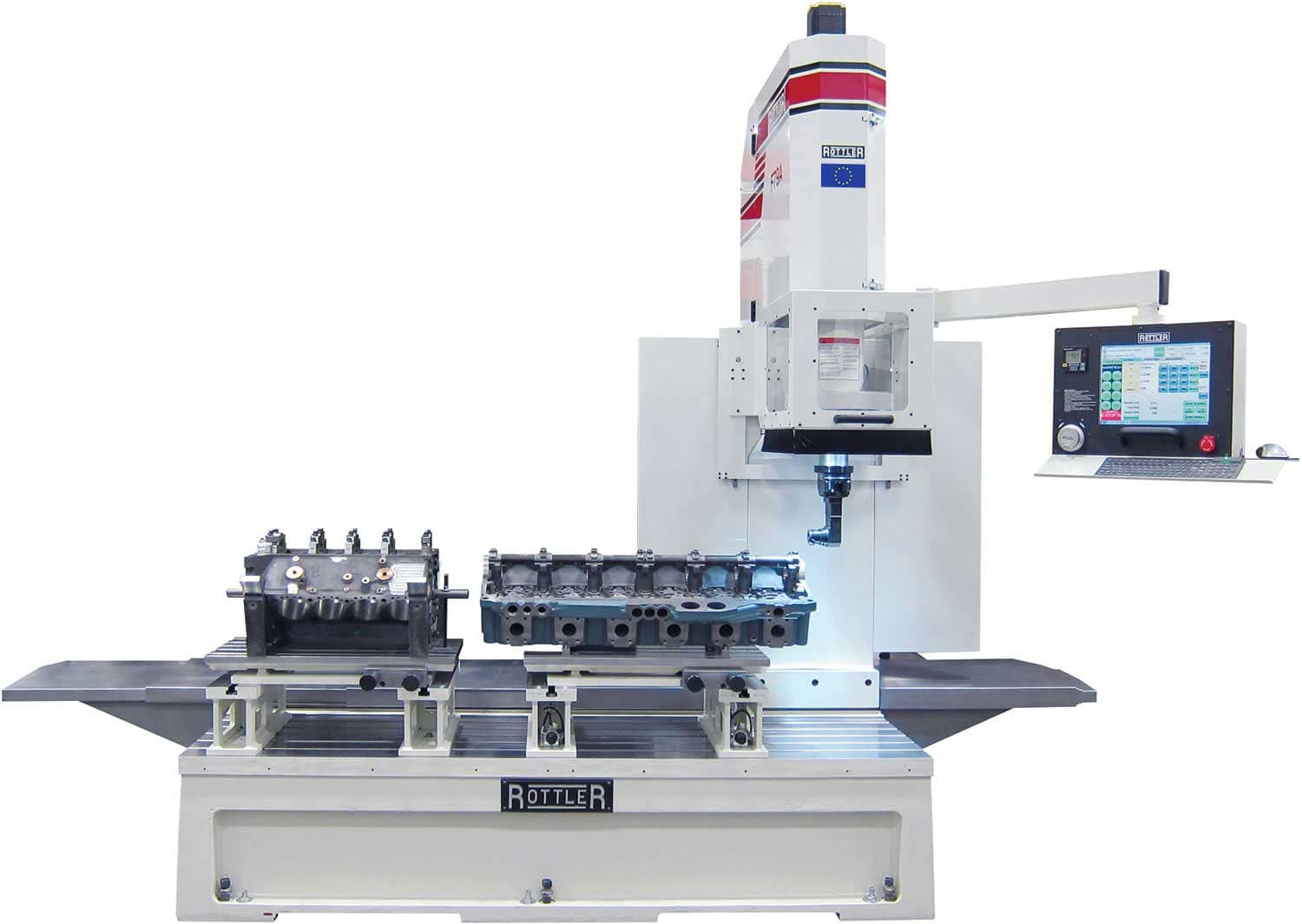
Rottler EM79 Multi-Purpose CNC Machining Center: Precision and Versatility
When it comes to advanced CNC machining technology, the Rottler EM79 Multi-Purpose CNC Machining Center stands out as a top choice for professionals in various industries. With its exceptional precision, versatility, and cutting-edge features, the EM79 delivers outstanding performance for a wide range of applications.
Precision and Accuracy
At the heart of the Rottler EM79 is its unparalleled precision and accuracy. This CNC machining center is engineered to deliver exceptional dimensional control and tight tolerances, ensuring consistent and high-quality results with every operation. Whether you’re machining complex parts or performing intricate tasks, the EM79 guarantees precision down to the finest detail.
Multi-Purpose Capabilities
The Rottler EM79 is designed to handle a multitude of machining tasks, making it a versatile solution for various industries. From automotive and aerospace to medical and energy sectors, this CNC machining center can accommodate a wide range of materials, including metals, plastics, and composites. With its multi-axis capabilities and advanced tooling options, the EM79 empowers users to tackle diverse projects with ease.
Efficiency and Productivity
One of the key advantages of the Rottler EM79 is its exceptional efficiency and productivity. Equipped with cutting-edge technology and intelligent automation features, this CNC machining center streamlines workflows, reduces setup times, and optimizes production cycles. With faster machining speeds and precise tool changes, the EM79 ensures that your operations remain efficient and cost-effective.
Advanced Features and Customization
The Rottler EM79 is packed with advanced features that enhance its performance and adaptability. From high-speed spindles and tool changers to integrated coolant systems and intelligent control panels, every aspect of the EM79 is designed to maximize productivity and user convenience. Moreover, Rottler offers customization options to tailor the machine to specific industry requirements, ensuring the perfect fit for your machining needs.
Reliability and Support
When investing in a CNC machining center, reliability and support are paramount. Rottler has built a reputation for delivering robust and durable machines that can withstand rigorous production demands. Backed by a dedicated customer support team and comprehensive warranty coverage, the Rottler EM79 offers peace of mind and ensures that your machining operations run smoothly and efficiently.
Discover the Rottler EM79 Difference
If you’re seeking a cutting-edge CNC machining center that combines precision, versatility, and efficiency, look no further than the Rottler EM79 Multi-Purpose CNC Machining Center. Visit our website at https://www.rottlermfg.com/general_purpose_cnc.php?model=EM79 to learn more about the EM79’s specifications, features, and customization options. Experience the difference of Rottler engineering and take your machining capabilities to new heights with the EM79.
We have more then 100 years of experience
We have more then 100 years of experience
Features
- Windows Touch Screen Operating System – Rottler uses Windows Touch Screen Technology on a 19″ touch panel. The Windows software has many advantages such as it’s common user interface that is easy to learn and fast to operate.
- Instant Internet Support – Rottler offers cutting edge internet support direct from your machine to the factory. Skype is installed for internet support. This feature gives you instant, direct contact with Rottler right on the machine without even making a phone call.
- Automatic Tool Changer – Automatic Tool Changing System available for production machining applications.
- Traveling Column Design – Allows stationary work piece for increased accuracy.
- Extra Height Capacity – Easily handle medium size diesel blocks forincreased versatility.
- Large Turcite Coated Box Ways – Turcite coated bedways for reduced friction, longer life and better accuracy.
- Extra Long T-slot – Work Table for dual workstations and increased versatility
- World Standard CAT40 Spindle – For fast tool changing and worldwide versatility. Sliding Quill Spindle Design – For deep hole machining required for block work.
- Servo Motors – Offer maximum torque and performance throughout the RPM range for precise accuracy and increase productivity.
- Single Phase 208-240V – For power efficiency that saves electrical running costs.
- Automated Workhead Tilting System – Provides superior surface finish.
- Extra Long T-slot Work Table – for Dual Workstations and Large Blocks for increased versatility.
- Direct Drive Precision Ball Screws – Give long trouble free life and accurate movement.
Machine Operations
- Automatic Tool Changer
- Block Surfacing
- Blue Print Boring
- Boring & Sleeving
- Circular Interpolation
- Connecting Rod Boring
- Cylinder Boring
- Cylinder Head Resurfacing
- Lifter Boring
- Line Boring
- Multi Purpose CNC (Custom Parts)
- Thrust Cutting
Download documentation
Rottler EM103H Standard Equipment
Standard equipment that comes with the Rottler EM79 Multi-Purpose CNC Machining Center:
- CNC (Computer Numerical Control) Machine using Windows Operating System and Industrial PC with Intel Processor. Precision Programming and Control thru a 15″ (400mm) Computerized Touch Screen.
- Software options available for Programmable & Automated Cycles such as Boring, Surfacing, Lower Sleeve Offset Boring, Water Hole Repairs, Main & Cam Line Boring, General CNC Machine Work
- USB flash drive for file transfer to and from computer
- Internet connection to the machine computer must be provided for training support and service.
- Machine/Computer can operate in either inch or metric system
- 3 Axis movement by Direct Drive Precision Ball Screws
- All motors – AC Servo Motors – Infinitely Variable
- Horizontal Movement (X Axis) – Left and Right Direction – 72” (1830mm)
- Horizontal Movement (Y Axis) – In and Out Direction – 12” (305mm)
- Vertical Movement (Z Axis) – Up and Down – 18” (457mm)
- Vertical, Horizontal and Spindle Load Monitoring for Fast Overload Shut Down
- Precision Position Display in .0001″ (.002mm) Resolution.
- Electronic Handwheel for manual movement – per click: Coarse Mode .01″ (.25mm) Medium Mode .001″ (.01mm) Fine Mode .0001″ (.002mm)
- Infinitely Variable Feedrates adjustable by handwheel during automatic cycles
- High Performance Spindle Rotation AC Brushless Servo Motor and Drive System
- Hard Chromed Precision Spindle with High Speed Angular Contact Bearings
- CAT40 Spindle Taper with Pneumatic Quick Change Tool System
- Fast Rapid and Jog Speeds for Reduced Cycle Time
- Automatic Workhead Tilt System for Back Clearance during Surfacing
- One Piece Heat Treated Mehanite Cast Iron Machine Castings
- Air Pressurized Column for Less Friction and Accurate Positioning
- Turcite Coated Slideways for Low Friction and Extended Life
- Automatic Central Lubrication System monitored by computer
- LED Work Light (mounted)
- Chip Guard with Adjustable Pivot Arm
- Operation, Programming and Spare Parts Manual – Digital
Give us a call, we have all the answers for you.
Rottler EM69HP specifications
Control | Automatic |
Touch Screen | 381mm |
Machine Height | 2989mm |
Table - Size | 2325 x 575mm |
Table - T Slots | 5 |
Travel - Horizontal (X Axis) | 1829mm |
Travel - In/Out (Y Axis) | 355mm |
Travel - Vertical (Z Axis) | 457mm |
Travel - Spindle Nose to Table | 1027mm |
Travel - Spindle Center to Column | 551mm |
Spindle - Taper | CAT 40 |
Spindle - Diameter | 96.5mm |
Spindle - Rotation Speed | 0 to 2000 RPM |
Spindle - Motor | 4.5 Kw |
Tool Changer | Optional |
Cylinder Bore Range (with Optional Cutterheads) | 19 - 178mm |
Line Bore Range (with Optional Cutterheads) | 48.5 - 150mm |
Surfacing Cutterhead Diameters | 250, 360, X & Xmm |
Dimensions - Machine | 1745D x 3877W x 2989mm H |
Dimensions - Floor Space Requirements | 2388D x 3877Wmm |
Dimensions - Shipping | 2235D x 2972W x 2286mm H |
Machine Weight | 4845 kg |
Electrical Requirements | 208-240V, 50A, 50/60Hz, 3Ph |
Air Requirements | 28 l/min @ 6 bar |
Paint Color Code | RAL9002 (Grey White) |
Control
Fixtures
Rottler Exclusive Touch Screen Programming: Streamlining Precision and Control
Experience the power of Rottler’s Exclusive Touch Screen Programming, designed to enhance precision and streamline control for your CNC machining needs. With the control pendant conveniently located, all machine controls are centralized, ensuring easy access and efficient operation. The touch screen interface intelligently displays only the buttons and interactive menus necessary for each specific machine operation, eliminating unnecessary clutter and simplifying the user experience.
Effortless Operation and Program Storage
Machine operations can be effortlessly performed, whether manually or automatically, thanks to Rottler’s Touch Screen Programming. This feature enables operators to execute tasks with ease, providing the ability to store programs in memory for future use. The convenience of program storage allows for quick access and consistent results, saving valuable time and effort in the machining process.
Real-Time Position Monitoring
The digital readout integrated into the Touch Screen Programming interface ensures accurate position monitoring at all times. Operators can rely on this feature to maintain precise control and make necessary adjustments as needed, resulting in superior machining outcomes. Additionally, the control system operates seamlessly in both metric and inch systems, accommodating diverse measurement preferences and requirements.
Unleash the Potential with Fully Programmable Cycles
Experience the freedom and versatility of fully programmable cycles with Rottler’s conversational 3-axis CNC control, powered by a PC-based system with the Windows Operating System. The intuitive touch screen interface empowers operators to program various parameters effortlessly. From setting program bore centers, exact depth, speed, feed, and more, to executing automatic cycles that efficiently machine complete banks or main lines, Rottler’s Touch Screen Programming opens up a world of possibilities.
Advanced Capabilities for Specialized Machining
Rottler’s Touch Screen Programming unlocks advanced capabilities for specialized machining requirements. Lower Offset Boring enables seamless repair of lower sleeves within the automatic cycle, while Circular Interpolate Counterbores allows for radius undercutting or wide counterbores. Achieve superior surface finish with the Multiple Pass Surfacing/Milling program, enabling rough cut and finish cut operations. Line Boring becomes effortless as the control system automatically moves from bore to bore, completing the line unattended. Additionally, the Rottler Circular Interpolation software ensures precise alignment of face main line thrust faces to the centerline of the crankshaft.
Discover the Efficiency of Rottler Touch Screen Programming
Discover the efficiency, precision, and control offered by Rottler’s Exclusive Touch Screen Programming. With its user-friendly interface, real-time position monitoring, and fully programmable cycles, this feature revolutionizes CNC machining. To explore the full potential of Rottler’s innovative technology, visit our website or contact us today. Elevate your machining capabilities and achieve exceptional results with Rottler’s Touch Screen Programming.
Unlock Advanced Machining Capabilities with Rottler’s Specialized Fixtures
For comprehensive information on Rottler’s specialized fixtures, we invite you to explore our brochure, speak with your local representative, or contact us directly. Our range of fixtures enhances the capabilities of our machines, allowing for efficient and precise machining operations.
Automatic 4th Axis Block Roll Over Fixture
Rottler’s Universal Quick Load/Unload Automatic Rotate 4th Axis Fixture and Software revolutionizes the machining process. This innovative fixture enables computer-controlled rotation of the block or cylinder head during automatic machining cycles. The fixture’s 360-degree rotation capability facilitates unique machining tasks, including stroker clearancing, surfacing, boring, and lifter bore machining in a single setup. The pneumatically operated tailstock ensures quick and easy loading and unloading of heavy blocks, enhancing productivity and efficiency.
Connecting Rod Fixtures
Discover the power of Rottler’s patented Connecting Rod Fixtures, designed to handle large connecting rods on EM79 machines. Our boring fixtures enable surfacing and boring operations on both the big end and small end of connecting rods in a single setup, ensuring perfect parallelism. Achieve precise center-to-center distances on all rods in a set, a crucial requirement for modern high-compression diesel engines. We also offer heavy-duty fixtures specifically designed for machining very large and heavy connecting rods found in natural gas compressors and workboat marine engines.
Dual Axis Leveling Table
Rottler’s patented Dual Axis Leveling Table and universal quick clamping system are perfect for surfacing, milling heads, blocks, and manifolds using CBN and PCD tooling. This innovative fixture allows for precise leveling adjustments in two directions, ensuring optimal clamping and surface alignment. With Rottler’s Dual Axis Leveling Table, any job can be clamped and leveled in seconds, minimizing stock removal and maximizing efficiency.
Explore Rottler’s Specialized Fixtures for Advanced Machining
Take your machining capabilities to new heights with Rottler’s specialized fixtures. Our commitment to innovation and precision ensures that our fixtures deliver exceptional results. To learn more about our fixtures and how they can enhance your machining processes, please refer to our brochure, get in touch with your local representative, or contact us directly. Discover the difference that Rottler’s specialized fixtures can make in your machining operations.