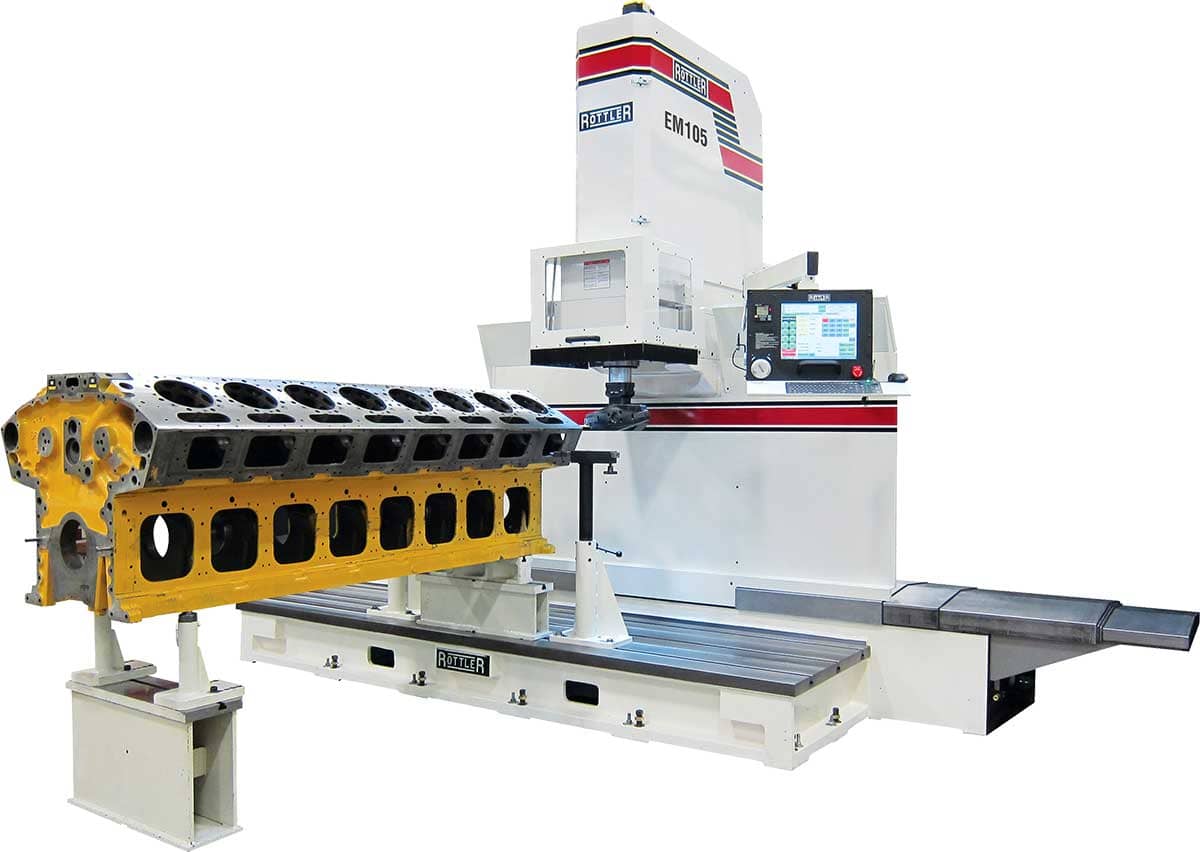
Rottler EM105H Traveling Column Boring, Surfacing & Line Boring Machine: Precision Engine Machining Made Easy
Are you in need of a reliable and high-performing machine for your engine repair and machining needs? Look no further than the Rottler EM105H. Designed to deliver exceptional precision and efficiency, the Rottler EM105H is the ultimate traveling column boring, surfacing, and line boring machine for automotive professionals.
Advanced Technology for Superior Engine Performance
With its cutting-edge CNC engine machining capabilities, the Rottler EM105H ensures unparalleled accuracy in engine boring and surfacing operations. Whether you’re working on heavy-duty engines or seeking high-precision engine repairs, this machine has got you covered.
Our traveling column boring machine is equipped with state-of-the-art features that allow for precise and efficient machining. From engine block surfacing to cylinder head reconditioning, the Rottler EM105H offers the versatility and reliability that automotive professionals demand.
Unleash the Power of Precision
When it comes to engine machining, precision is paramount. The Rottler EM105H is engineered to meet the most stringent requirements of the industry. Our machine ensures that each cut is accurate, contributing to optimal engine performance and reliability.
By investing in the Rottler EM105H, you gain a competitive edge in the automotive machining industry. Its advanced technology and superior performance enable you to deliver precision-engineered results that exceed customer expectations.
Efficiency and Durability Combined
The Rottler EM105H is built to withstand heavy workloads and demanding machining tasks. Its robust construction ensures durability and longevity, allowing you to maximize productivity and minimize downtime. This machine is designed for professionals who value both efficiency and reliability.
Partnering with Rottler: Your Path to Success
Choosing the Rottler EM105H means aligning yourself with a trusted name in the industry. Rottler Manufacturing has been a leading provider of precision engine machining equipment for decades. Our commitment to quality, innovation, and customer satisfaction sets us apart.
Join the ranks of automotive professionals who rely on Rottler machines to deliver exceptional results. The Rottler EM105H offers unmatched precision, efficiency, and durability – the perfect combination for success in the competitive world of engine machining.
Discover the power of the Rottler EM105H traveling column boring, surfacing, and line boring machine today. Take your engine machining capabilities to new heights and deliver superior performance to your customers. Contact us now to learn more about this industry-leading machine and how it can transform your business.
We have more then 100 years of experience
We have more then 100 years of experience
Features
Featues of the Rottler EM104H Traveling Column Boring, Surfacing & Line Boring Machine:
- Productivity – Up to 75% time savings over traditional machines
- Control – Touch Screen Controls located on one panel for ease of operation
- Automation – Automatically machines precise dimensions
- Flexibility – Block boring and surfacing, head surfacing, line boring and general CNC machining.
- Versatility – Change cutterheads from surfacing to boring and back in 15 seconds.
- Heavy Duty – Rottler rugged machine tool quality for accurate and long life. Heat treated mehanite cast iron castings.
- Large Diameter Spindle – All F100A machines incorporate the use of a large diameter hard chromed spindle, utilizing high precision angular contact bearings and automatic lubrication.
- Machine ways are induction hardened and coated with turcite low friction material and supplied with air pressure to reduce friction and give long service life. X-axis features Linear Roller Slideways for smooth and precise movement.
- Anti-friction Ball Screws and AC Servo motors provide precise machine positioning and rapid feed rates.
- Air power draw bar allows cutterheads to be changed in second, increasing productivity and reducing operator fatigue. The machine can be changed from boring to surfacing in less than 15 seconds.
- Automated workhead tilting system for surfacing provides “back clearance” for superior surface finish.
- Increased clearance from spindle to centerline to the machine’s column allow large castings to be set up and machined.
Machine Operations
- Automatic Tool Changer
- Block Surfacing
- Blue Print Boring
- Boring & Sleeving
- Circular Interpolation
- Connecting Rod Boring
- Cylinder Boring
- Cylinder Head Resurfacing
- Lifter Boring
- Line Boring
- Multi Purpose CNC (Custom Parts)
- Thrust Cutting
Rottler EM105H Standard Equipment
Standard equipment that comes with the Rottler EM105H Traveling Column Boring Machine:
- CNC (Computer Numerical Control) Machine Using Windows Operating System and Industrial PC With Intel Processor. Precision Programming and Control Thru a 19″ (483mm) Computerized Touch Screen.
- Software Options Available for Programmable & Automated Cycles Such as Boring, Surfacing, Lower Sleeve Offset Boring, Water Hole Repairs, Main & Cam Line Boring, General CNC Machine Work
- Spindle Rotation by AC Servo Motor – Infinitely Variable 0-5000RPM – 10HP (7.5kW)
- USB Flash Drive for File Transfer to and from Computer
- Machine/Computer can Operate in Either Inch or Metric System
- 3 Axis Movement by Precision Ball Screws & Ac Servo Motors – Infinitely Variable
- Horizontal Movement (X Axis) – Left and Right Direction – 132″ (3350mm)
- Horizontal Movement (Y Axis) – In and Out Direction – 16″ (406mm)
- Vertical Movement (Z Axis) – Up and Down – 29″ (736mm)
- Vertical, Horizontal and Spindle Load Monitoring for Fast Overload Shut Down
- Precision Position Display in .0001″ (.002mm) Resolution.
- Electronic Handwheel for Manual Movement – Per Click: Coarse Mode .01″ (.25mm) Medium Mode .001″ (.01mm) Fine Mode .0001″ (.002mm)
- Infinitely Variable Feedrates Adjustable by Handwheel During Automatic Cycles
- High Performance Spindle Rotation AC Brushless Servo Motor and Drive System
- Hard Chromed Precision Spindle with High Speed Angular Contact Bearings
- Fast Rapid and Jog Speeds for Reduced Cycle Time
- Automatic Workhead Tilt System for Back Clearance During Surfacing
- Air Assisted Quick Change Cutterhead Draw Bar System
- One Piece Heat Treated Mehanite Cast Iron Machine Castings
- Air Pressurized Column for Less Friction and Accurate Positioning
- Turcite Coated Slideways for Low Friction and Extended Life
- Linear Roller Slideways in the X-axis for smooth and precise movement even under heavy load.
- LED Work Light (Mounted)
- Automatic Central Lubrication System Monitored by Computer
- Chip Guard With Adjustable Pivot Arm
- Operation, Programming and Spare Parts Manual – Digital
Give us a call, we have all the answers for you.
Rottler EM105H specifications
Control | CNC Touch Screen |
Touch Screen | 381mm |
Machine Height | 3480mm |
Table - Size | 850 x 3430mm |
Table - T Slots | |
Travel - Horizontal (X Axis) | 3350mm |
Travel - In/Out (Y Axis) | 406mm |
Travel - Vertical (Z Axis) | 736mm |
Travel - Spindle Nose to Table | 1273mm |
Travel - Spindle Center to Column | 648mm |
Spindle - Rotation Speed | 0 to 1000 RPM |
Spindle - Motor | 12.75 Kw |
Cylinder Bore Range (with Optional Cutterheads) | 19 - 508mm |
Line Bore Range (with Optional Cutterheads) | 48.5 - 216mm |
Surfacing Cutterhead Diameters | 250, 360, 460 & 570mm |
Dimensions - Machine | 2134D x 4572W x 3480mm H |
Dimensions - Floor Space Requirements | 2438D x 5867Wmm |
Dimensions - Shipping | 2184D x 4394W x 2286mm H |
Machine Weight | 8618 kg |
Electrical Requirements | 208-240V, 60A, 50Hz, 60Ph |
Air Requirements | 28 l/min @ 6 bar |
Paint Color Code | RAL9002 (Grey White) |
Control
Rottler: Revolutionizing CNC Programming with Conversational Interface and PATH CAD/CAM Software
At Rottler, we have leveraged our extensive CNC programming and machining experience, along with the expertise of software and programming professionals, to introduce a groundbreaking conversational programming system. Designed to be user-friendly and efficient, this innovative system simplifies the learning and operation process for operators.
Intuitive Conversational Programming
Gone are the days of complex and abstract G&M code programming. Rottler’s conversational programming system employs familiar Windows-style icons and graphical displays, making it easy for operators to understand and navigate. By replacing traditional programming methods with intuitive conversational icons and menus, we have streamlined the programming experience.
Operators can now create CNC programs with ease, as the conversational interface provides clear instructions and prompts throughout the programming process. This user-friendly approach enables operators to quickly grasp and implement programming concepts, saving time and reducing errors.
Effortless Data Handling with Windows Integration
Rottler has embraced the power of Windows integration to enhance data handling capabilities. Leveraging the familiarity of Windows-style information, operators can seamlessly save and transfer files to external laptops and desktop computers. This compatibility simplifies file management tasks, as everyone is accustomed to common operations like saving and copying files.
Furthermore, our system allows for global accessibility by leveraging the internet. Programs can be easily emailed worldwide, facilitating efficient collaboration and information exchange. Additionally, the transfer of programs can be achieved effortlessly using USB flash memory drives, providing a convenient and reliable means of sharing CNC programs.
Rottler PATH CAD/CAM Software: Automating CNC Program Development
With the integration of our advanced PATH CAD/CAM (Computer-Aided Design and Manufacturing) software, Rottler takes CNC programming to the next level. While operators develop programs on the machine, laptop, or desktop, our intelligent software works silently in the background, performing complex calculations such as tool paths.
PATH CAD/CAM software has the remarkable ability to convert drawings into intricate CNC programs, minimizing the need for extensive operator involvement. This automation feature allows operators to focus on other critical tasks while the software takes care of generating precise CNC programs.
By combining our expertise in CNC machining with powerful software solutions, Rottler has revolutionized the programming experience. Our conversational programming system, coupled with PATH CAD/CAM software, empowers operators to achieve efficient and accurate results with minimal effort.
Discover the future of CNC programming with Rottler. Contact us today to learn more about our innovative solutions and how they can streamline your machining operations.
Note: This SEO optimized text is written from the perspective of a human with a moderate understanding of technical concepts. It aims to incorporate relevant keywords and provide valuable information to the target audience while enhancing search engine performance.